To solve the complex fluid problems of today, the industry can no longer rely on the tools of yesterday. Enter next-gen CFD software.
Researchers, engineers and scientists have already answered the easy questions.
As time passes, the questions—and the physics—get more and more intricate. To push the limits of what we can solve, to get to where we need to be faster, we need to move into the next generation of computational fluid dynamics (CFD). Because running simulations the same old way—remaining unchanging in the way we learn new things—will in fact not allow the industry to really change or learn.
Especially when the world needs it most.
Nothing has proved the need for next-gen CFD software quite like the COVID-19 pandemic. Pharmaceutical companies were asked to rapidly develop and produce life-saving vaccines in record time. To do that, there was only one way forward: next-gen CFD software. Without it, drug developers wouldn’t have been able to accurately predict the complex, multi-fluid mixing processes that allowed them to scale-up production and bring these compounds to market (at a fraction of the time and cost).
Pharma companies like Pfizer, Bristol Myers Squibb and AbbVie are already one step ahead with nextgen CFD software. It’s critical that other experts—across other industries and applications—follow their lead. Because someone else will, and your research or company will get left behind.
But what even is next-gen CFD software? In this guide, we will:
- Trace the origins of CFD software and its initial applications.
- Show the power of modern CFD software.
- Discuss the future of CFD software.
Where We’ve Been: The Origins of CFD Software
To understand next-gen CFD software, we need to understand where CFD came from, what it’s traditionally been used for and how that use has changed and grown over time.
What Is CFD Software?
CFD is a method many engineers, scientists and researchers use to mathematically model and solve momentum, energy and mass transport fluid flow problems.
If you’ve ever seen a wind tunnel, then you’ve seen a fluid dynamic modeling application.
Through The Years
The 17th Century
Scientists and researchers have always been fascinated with fluid dynamics, and through the years many have tried to mathematically describe the motion of fluids. One could argue that the roots of computational fluid dynamics software stretch all the way back to the 17th century when Sir Isaac Newton tried to quantify and predict fluid flow phenomena through his Newtonian physical equations.
The 19th Century
Navier-Stokes equations came next in the early to mid 1800s, and they define many singlephase fluid flows. These equations were built upon the application of Newton’s second law to fluid motion. They were created and iterated throughout those decades by Claude-Lewis Navier and then later by George Gabriel Stokes (thus the name). For many decades after, the Navier-Stokes equations became the basis of fluid dynamics research.
The 20th Century
But how did this field of research go digital?
In the late 1960s, the concept of a “digital twin” was introduced by NASA as part of the Apollo program. Researchers developed two identical space vehicles where one of the two was used as a “twin” to simulate the real-time behavior of the counterpart that was sent to space. Digital twins are now used in a variety of applications to replace physical experiments so that they can be run “in silico,” meaning by means of computer modeling.
Digital twins save time and money, and when they’re high quality, they can completely replace physical experiments—but more on this later.
Coincidently, the first CFD algorithms were developed around this same time as the digital twin concept, and it was around this time when many agree the modern definition of CFD begins. These first CFD algorithms were used to model flow over airfoils, ship hulls and aircraft fuselages. These models and methods could be integrated to generate numerical solutions based on hand calculations. And as early computers came to form, hand calculations moved to computer-based calculations.
Ultimately, the development of computational fluid dynamics software for commercial use began in the 1980s, after Boeing, NASA and other organizations released codes to the public. The success of these models to aerospace and naval hydrodynamics lead to the commercialization of many CFD packages in the 1980s and 1990s, which were initially targeted to users in the automotive, defense and energy industries.
The 21st Century
Moving into the 2000s, commercial CFD packages trickled into the pharmaceutical and biopharmaceutical industries with newer, more complex algorithms designed to address the needs of a 3D mixing environment.
What Is CFD Used For?
CFD software is used to predict and simulate fluid flow, heat transfer, species transport, chemical reactions, particle transport and rigid-body dynamics among other physical processes that would otherwise be too time-consuming, complex and expensive to investigate using experimental approaches.
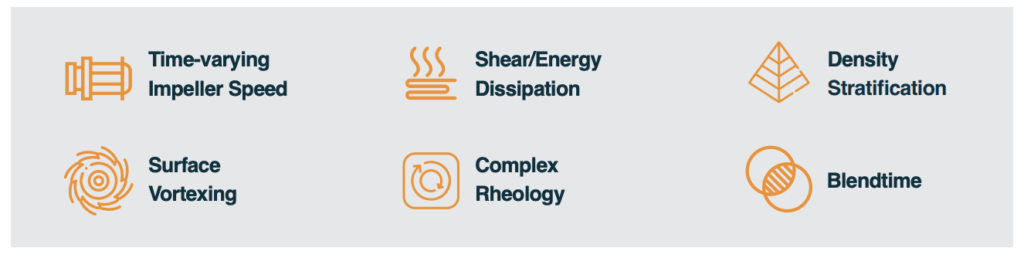
As stated in the history above, CFD has been used for aerodynamics and hydrodynamic modeling in the automotive, aerospace and naval industries for a while now. Slowly these functions have been built upon and applied to more complex uses in turbulent, mixing environments, which have found beneficial application in the pharmaceutical and food industries.
Instead of a single stream of air or fluid, think mixing, sloshing and shaking multiple fluids in geometrically complex containers. As you can imagine, these types of models are much more difficult to calculate, requiring more refined algorithms and a lot more computing power to recreate with any amount of useful fidelity, which leads us to the next question.
What Are Its Limitations?
While traditional CFD software is able to answer those singlephase fluid flow applications, it struggles with more complex mixing problems.
Time-average models provide sufficient fidelity for single-phase/ single fluid systems in those first use cases. But extending the models to handle the multi-phase, transient and multi-fluid system typical of pharmaceutical manufacturing applications prove difficult—and costly.
Because these original CFD implementations are focused on steady-state flow fields, they provide little insight into the turbulent structure and flow field driving reactions, mixing and cell damage processes.
Limitations of Traditional CFD Software?
– Low computational speed
– Takes days to generate 1 second of simulation time
– Takes weeks to prepare simulation inputs
– Requires more modeling assumptions
Additional challenges are presented by topologically complex systems, which often require geometry clean-up and careful volume meshing. Moreover, although some academic circles can extend these traditional CFD tools to handle multiphase flows, the industrial application of CFD to generalized bioreactor design and process simulation is not widespread.
Thus, although time-averaged CFD could provide insights into aspects of a process, it is not a practical tool for fully simulating processes. As a result, physical experiments are still a requirement for scale-up, which lengthens production times and costs more money.
The limitations of traditional CFD software have pushed the industry to innovate in order to solve more complex problems faster. Let’s take a look at what this next generation of CFD modeling looks like.
Where We’re At: Next-Gen CFD Software
CONFESSION:
“Next-Gen CFD” is a bit of a misnomer. The term “next-gen” somewhat implies a future-state, but really, we’re already living with next-gen CFD software. Just ask companies like Pfizer, BMS and Dow Chemical.
The capabilities of modern CFD software are leaps and bounds above what traditional modeling software programs are capable of.
What’s Different About Next-Gen CFD Software?
There are a few factors that make this generation of CFD software different from previous iterations, and worthy of the title of “next-gen.” Let’s get into them.
Modern Algorithms
Modern computational fluid dynamics software is based on lattice-Boltzmann algorithms, which solve the time-dependent Navier-Stokes equations.
Modern algorithms provide high grid fineness, allowing for more complex physics.
Unlike legacy CFD tools that describe time-average/steadystate flow fields using low-fidelity turbulence models, latticeBoltzmann is a mesoscopic modeling tool that describes the space-time dynamics of a probability distribution function across phase-space.
Instead of solving the Navier-Stokes equations directly, fluid density is simulated on a lattice with streaming and collision properties. This modeling method more accurately mimics the real behavior of a fluid.
This approach, which is inherently time-dynamic, enables superior turbulence modeling capabilities, faster run times and scales more favorably with increasing system complexity. Traditional impediments like porous media and complex geometry are no longer a factor that holds a simulation back.
Modern GPU Architectures
For these modern algorithms to work, though, they need to be paired with modern graphical processing card architectures (GPUs).
GPUs provide significantly computational power, allowing users to maximize the amount of science they can do per unit man-hour.
The Power of Next-Gen CFD Software
– Model millions & billions of grid points
– Run millions & billions of updates per second
If grid fineness informs physics complexity, speed informs practicality. That’s where GPUs come in. GPU-based algorithms help users model transient, three-dimensional physics in real-time.
Many self-proclaimed “modern” CFD solutions are coded for CPUs (central processing units). So, if you want more accurate results, faster, you need next-gen CFD software that has been coded specifically with GPU-based algorithms.
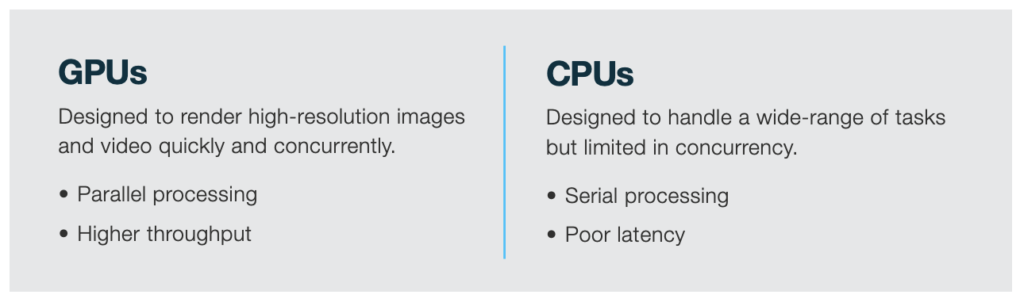
Easy User Setup
On that note about practicality: CFD software is only as useful as it is usable. It’s no good if it takes too long to learn how to add geometries, set up models and generate results. You need something that can help you start visualizing your simulation after just minutes of processing time.
Here are capabilities that indicate ease of setup:
Import Low-Quality or Imperfect Geometry Files
When it comes to setting up the simulation, your tool should allow you to focus on what matters without getting bogged down by CAD shape healing or meshing complex geometries.
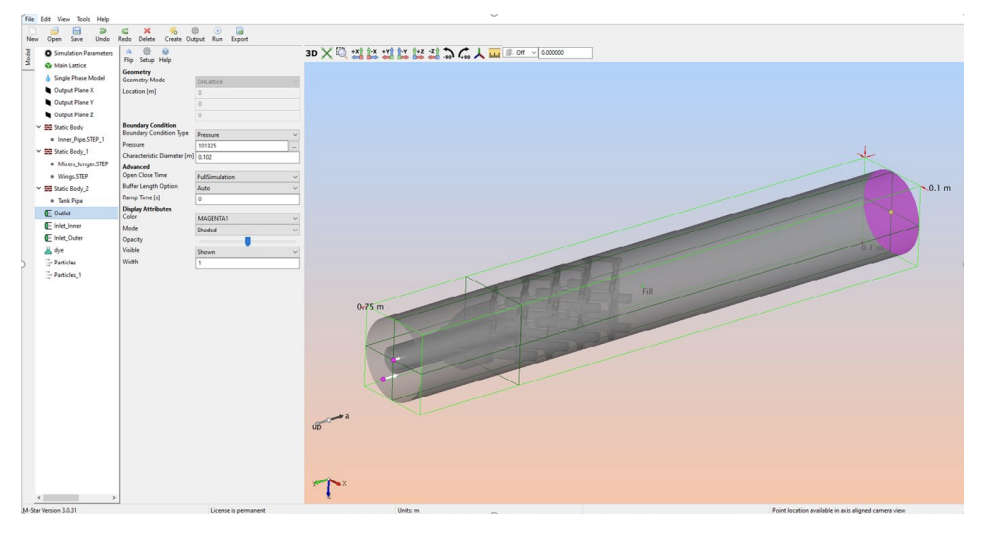
Use Existing & Custom Fluid Models
By itself, the combination of a lattice-Boltzmann CFD solver and high-resolution meshes should provide the basis fluid model for your simulations that you can then layer and enrich with additional, extraordinary physics. Because you already have a baseline fluid model, you can focus more on adding complexity to the problem and ultimately solving these problems faster.
Analyze Data In Real-Time
Imagine how much faster you can get results if you can analyze data as it’s generated in real-time by the solver. With modern CFD software that offers an integrated post-processing suite, you can.
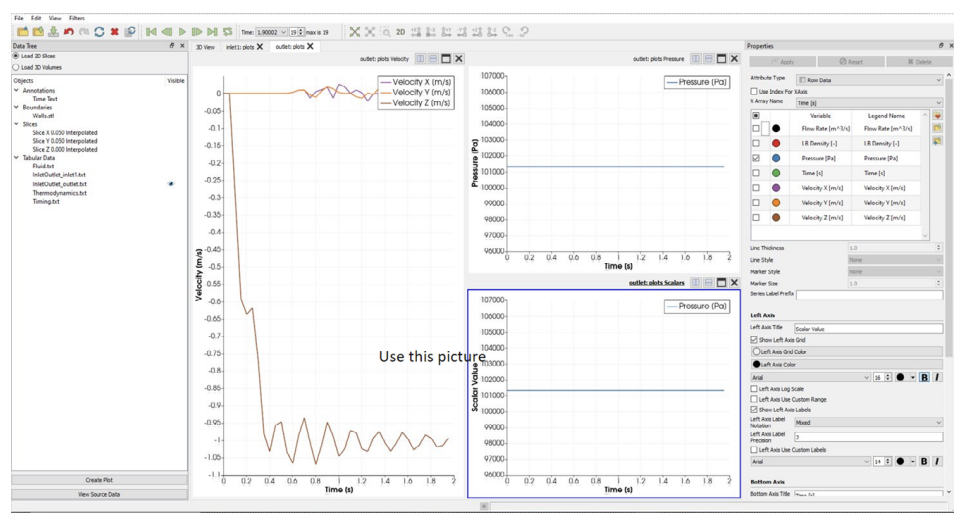
Where We’re Going: The Future State of CFD
CFD software has come a long way, helping engineers, scientists and researchers in the pharmaceutical space and beyond solve more complex physics problems—faster and at an accuracy that rivals experimental data. At this rate, imagination is the only limiting factor to how these tools can be applied.
What’s Possible with Next-Gen CFD?
There are many ways that this software can be applied, and businesses and research institutions have only just scratched the surface.
Answer Questions Like:
– What dosage is needed to effectively deliver an inhaled drug to the lungs?
– How is oxygen transferred in stirred tank bioreactors?
– What thickness should the coating be on a new pill to minimize breakage and reduce operating time?
As discussed throughout this guide, the pharmaceutical industry is a fertile ground for use-cases of next-gen CFD modeling.
For example, biomanufacturing processes that produce biologic drugs is an important area of study. These biologic drugs are typically produced by living organisms within stirred tank bioreactors, requiring a continuous supply of sparged oxygen.
However, oxygen transfer in bioreactors is governed by complex fluid mechanics, which causes challenges when it comes to scaling up from lab-scale, tabletop bioreactors with small operating volumes to productionsized bioreactors that can hold up to tens of thousands of liters.
Are You Wasting Time & Money?
Constant improvement is the lifeblood of successful and innovative companies. Sticking to legacy systems only breeds stagnation. If your company uses legacy CFD or physical experiments for scale up and process development, you’re wasting the two things a business cannot afford to waste: Time and money.
Especially now, when problems can appear suddenly and solutions need to account for production on a global scale.
Your Bottom Line Is On the Line
With next-gen software, the setup and execution of fluid simulations no longer take days and weeks like its legacy counterparts. Successful, applicable and high-fidelity simulations are running in hours and minutes.
These faster, more-accurate simulations allow companies to design, test and scale-up production faster than ever.
Get a leg up on your competition. Get to market quicker. No matter what you’re using next-gen CFD software for, it will greatly affect the bottom line of your company. That’s what you stand to gain.
Conclusion
The need for more efficient process scale-up and optimization strategies within industries like pharma is pressing. Thankfully, the next generation of CFD software is already here to address these needs.
The industry is more than ready for next-gen CFD software—it’s time to embrace it. Using it will reward users with data-rich solutions to complex, multi-physics problems. But ignoring it will leave your questions unanswered.